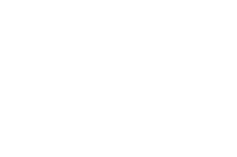
热塑性聚酰亚胺TPI
热塑性聚酰亚胺(TPI)是在传统热固性PI的基础上开发的,与热固性PI相比,TPI具有许多潜在的优势。
1、TPI具有出色的加工性能、韧性和耐损伤性,生产周期短、操作简单以及制造成本低等优势。
2、TPI 可熔化和重新加工,因此可以通过加热和加压来修复受损结构。
3、TPI在环境友好方面具有优势,它是完全酰亚胺化的聚合物,不包含反应性化学物质,因此毒性非常低。
TPI加工生产工艺
对于热塑性聚合物的加工,普遍的有3种工艺,分别是注塑、模压、挤出。
1)注塑成型工艺
所谓注塑成型(Injection Molding)是指将已加热融化的材料喷射注入到模具内,经由冷却与固化后,得到成形品的方法。也叫射出成型,适用于量产与形状复杂产品等成形加工领域。
注塑成型工艺的优点:
A、废料损失少。
B、成型后不需要继续完善零件。
C、成型周期短。
注塑成型工艺的缺点:
A、零件必须按照特定的成型要求进行设计。
B、注塑零件可能存在熔合缝。
C、不能注塑壁厚较大的产品,容易出现收缩孔。
D、适合批量大的产品,批量少的产品浪费较大。
热塑性聚酰亚胺(TPI)的注塑成型工艺相对来说比较成熟,但是仍旧存在较大的局限性,例如不适合注塑大型零件的产品,注塑后的收缩孔会显著影响产品的使用。
2)模压成型工艺
模压成型中,把一定量通常被预热的塑料(可以是粉状、粒状或片状等)置于被加热的模具型腔内,然后合上模具,对塑料施加压力,使之熔融成为粘流态而充满模腔,成型为制品;制品固化后,开模,取出制品。
模压成型的优点:
A、制品的内应力很低,且翘曲变形也很小,机械性能较稳定。
B、模腔的磨损很小,模具的维护费用较低。
C、可成型较大型平板状制品。模压所能成型的制品的尺寸仅由已有的模压机的合模力与模板尺寸所决定。
模压成型的缺点:
A、整个制作工艺中的成型周期较长,效率低,对工作人员有着较大的体力消耗。
B、不适合对存在凹陷、侧面斜度或小孔等的复杂制品采用模压成型。
C、对有很高尺寸精度要求的制品(尤其对多型腔模具),该工艺有所手短。
热塑性聚酰亚胺(TPI)模压成型工艺相对来说比较成熟,更加适合做一些厚壁的板材,后续再采用机加工的形式加工成所需的零件。现场市场上基本更多的都是采用这种工艺来生产TPI的板材,但是,其成型周期较长,效率低的加工方式带来的是批量生产较慢,加工费用偏高。此外,采用模压成型的方式不能保证棒材、管材的成品率,相对增加了客户端的使用成本。
3)挤出成型工艺
挤出成型又叫挤塑、挤压、挤出模塑。是借助螺杆和柱塞的挤压作用,使塑化均匀的塑料强行通过模口而成为具有恒定截面的连续制品。
挤出成型的优点:
A、设备制造容易,成本低。
B、可以连续化生产,生产效率高。
C、设备的自动化程度高,劳动强度低。
D、生产操作简单,工艺控制容易。
E、挤出产品均匀、密室,质量高。
挤出成型的缺点:
A、不能生产三维尺寸的制品。
B、开机所需原料成本较大,一次开机往往需要几十甚至上百公斤。
热塑性聚酰亚胺(TPI)挤出成型工艺相对来说不够成熟, 由于热塑性PI热稳定性较差,易降解和水解,并且伴有严重的离模胀大效应等问题,直接影响了热塑性聚酰亚胺(TPI)的连续性挤出的生产化,导致国内几乎没有厂家能够实现聚酰亚胺(PI)型材的连续挤出成型。TPI在挤出时需要比较严苛的加工条件,挤出温度、成型压力等加工窗口较窄。挤出成型工艺能够大幅度缩短成型周期,且连续化的生产能够保证产品一致性、稳定性较好。
江苏君华特种工程塑料制品有限公司通过长时间摸索,已能够成熟稳定地连续挤出热塑性聚酰亚胺(TPI)型材。
TPI的产业应用
机械工业:TPI具有优异的力学性能与耐摩擦性,可替代钛合金用于制造各种零件,例如发动机内盖﹑致密零件﹑离合器齿圈等。
航空航天:TPI具有良好的阻燃性能,可以减少飞机因火灾而导致的损害。
电子通信:TPI在高温﹑高压和高湿度等恶劣的工作环境下可以保持良好的电气绝缘性,通常用于制造晶圆载体、电子绝缘膜片和各种连接的设备。
医疗:由TPI树脂制成的人造骨具有质轻、无毒、抗腐蚀性强的优点。
电力:TPI具有良好的热稳定性与介电性,可以用来生产电线电缆等各种电力装备。
涂料:在金属表面覆盖TPI的细粉涂料可获得具有优异绝缘性、较强耐腐蚀性﹑耐热性和耐水性的TPI粉末金属涂料产品,广泛用于化学防腐、家用电器、电子产品、机械等领域。
江苏君华特塑
江苏君华特塑16年来致力于PEEK、PI等高性能特种工程塑料的研发、生产、销售,拥有丰富的协同研发、样品测试、批量生产、技术支持及售后服务保障等经验,期待以我们的知识与能力,为您提供PEEK、PI等各应用领域的长期应用解决方案。